Introduction
In part one of Jo’s story, we heard about her background and the origins of Petal and Plume as a business. This time around, she tells us about the process of making her handmade resin jewellery, along with some of the hazards!
This is part two of a three-part story.
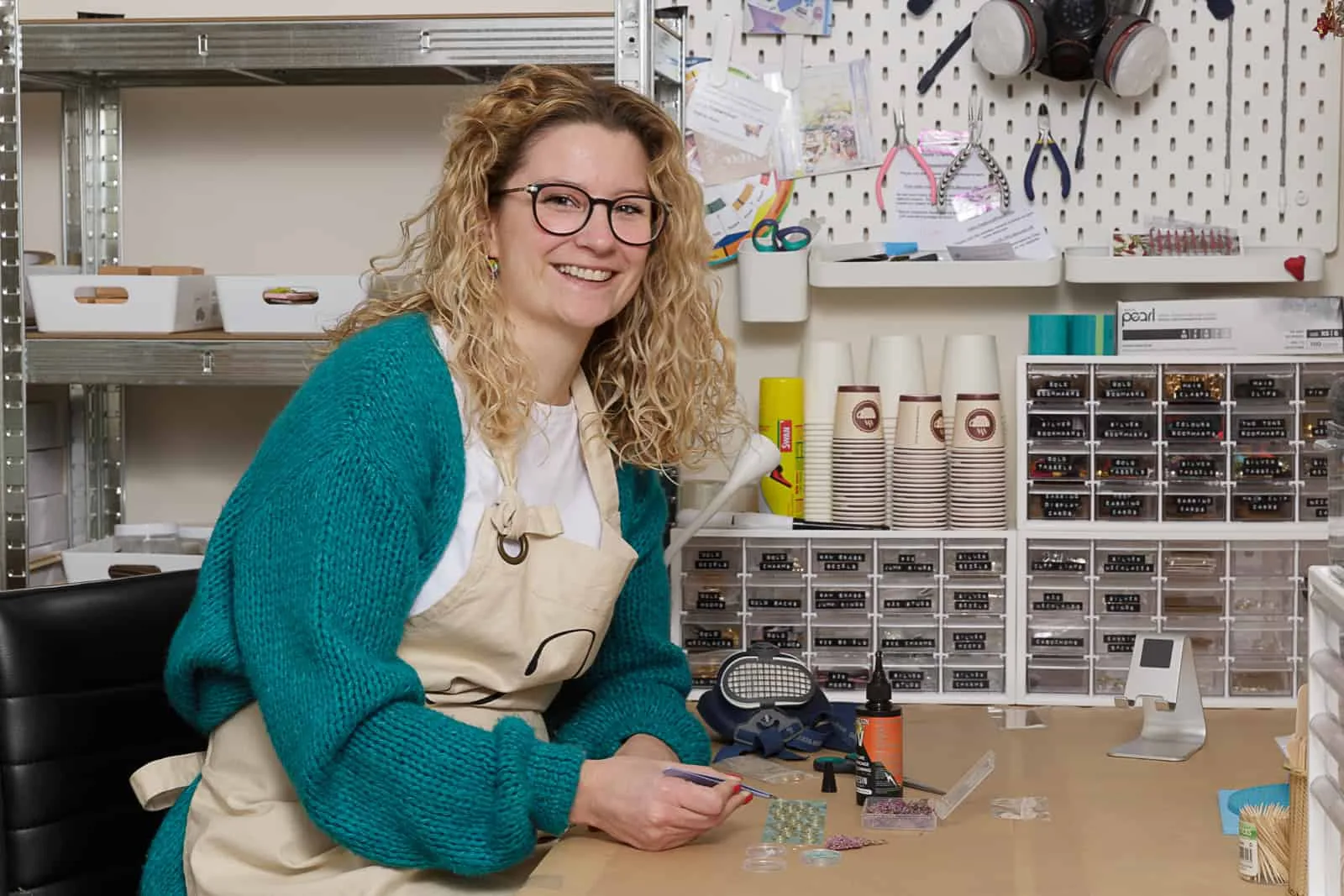
Are you self-taught or have you undertaken any specialist training?
I’m self-taught, but when I carried out my own experiments for fun, I soon reached a point where if I was going to do resin craft as a business, I realised that I would need to know a lot more. That’s when I reached out to Lou [Create & Bloom] for some one to one training.
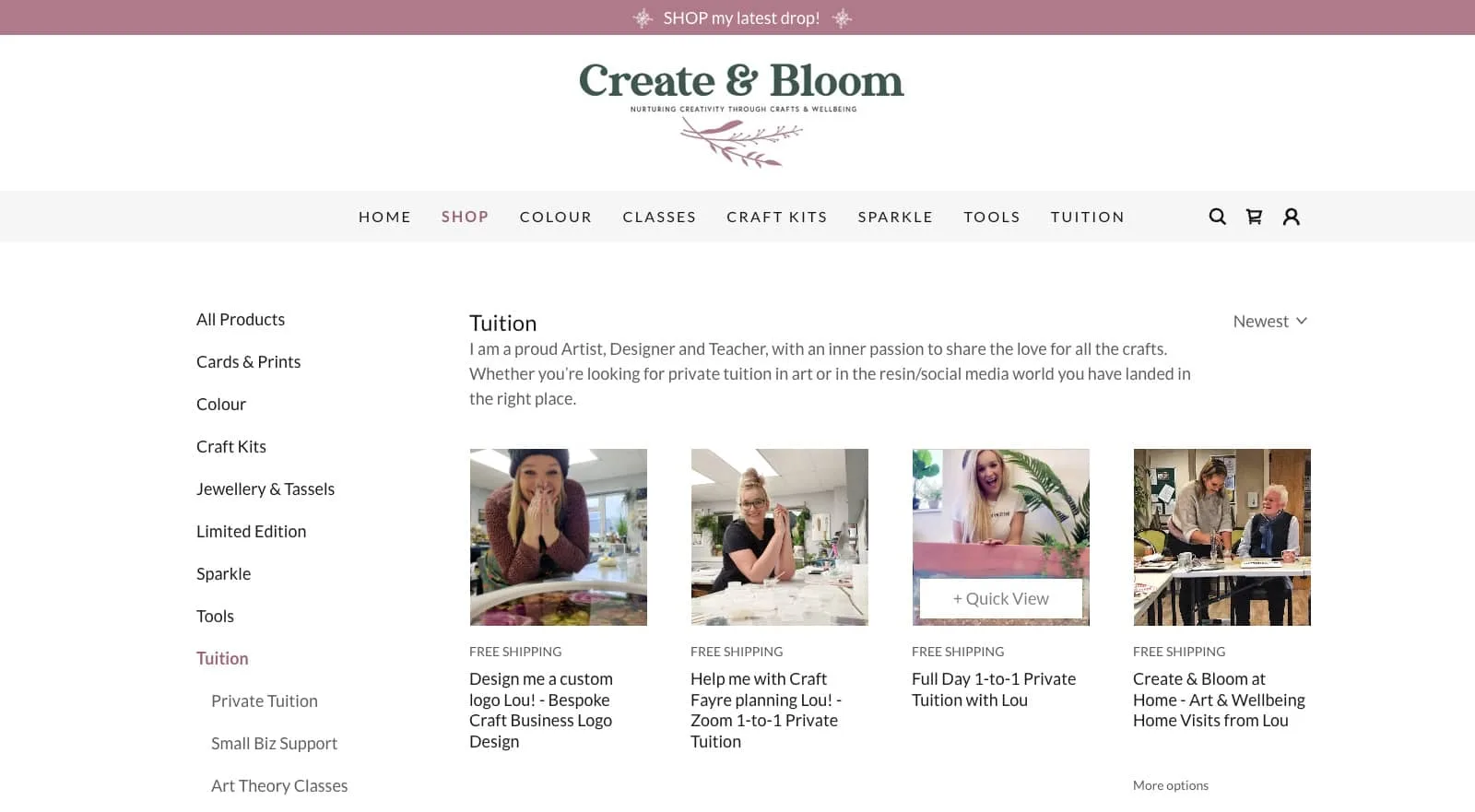
Create and Bloom Crafts: Tuition & Workshops [ https://createandbloomcrafts.com/shop/ols/categories/tuition]
Lots of mistakes along the way I guess?
I can laugh about it now of course, but I can remember the first batch of resin that I made. My girls were so impressed, but it was still sticky because it hadn’t cured. There’s so many parts to the process that I didn’t know about when I started out. I can remember putting some bits in the freezer thinking that it might dry them out faster [laughs]. Even with instructions, it wasn’t quite as straightforward as advertised. It would say on the resin packaging, stir for three minutes. So I stirred for three minutes, but it didn’t work. Then you learn, through experience, when it’s right, despite what the instructions say.
Sounds a lot like cooking
That’s probably the best analogy. Different temperatures, varying quantities and combining different ingredients such as glitter and colour pigments, all affect the working process. So, just like cooking, you’re constantly learning. It started all over again when I began using the Ultra Violet [UV] sensitive resins.
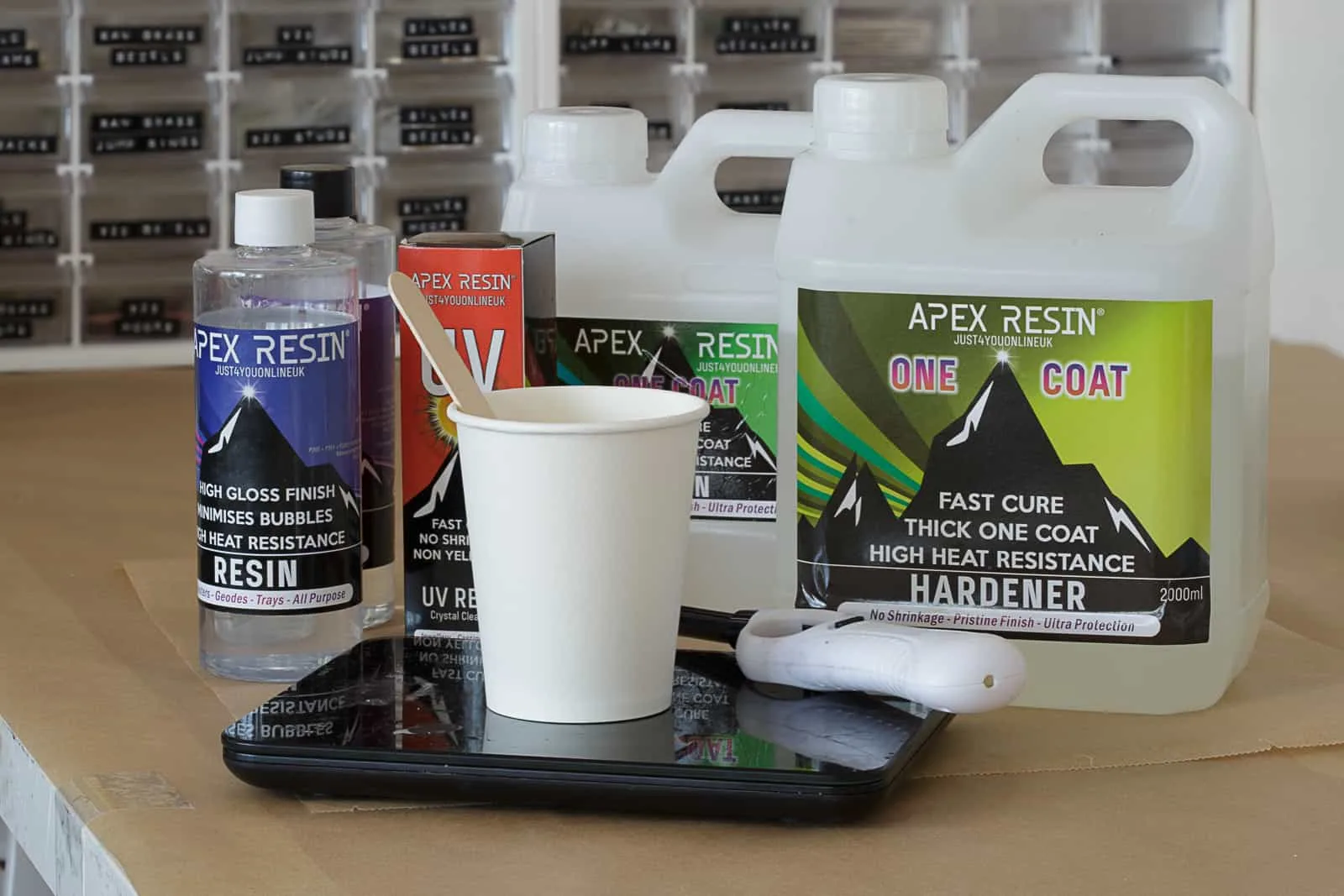
How do you buy the resin? Is it flakes or liquid or …
It’s a liquid which comes in two parts. When mixed together, that’s when the curing process starts.
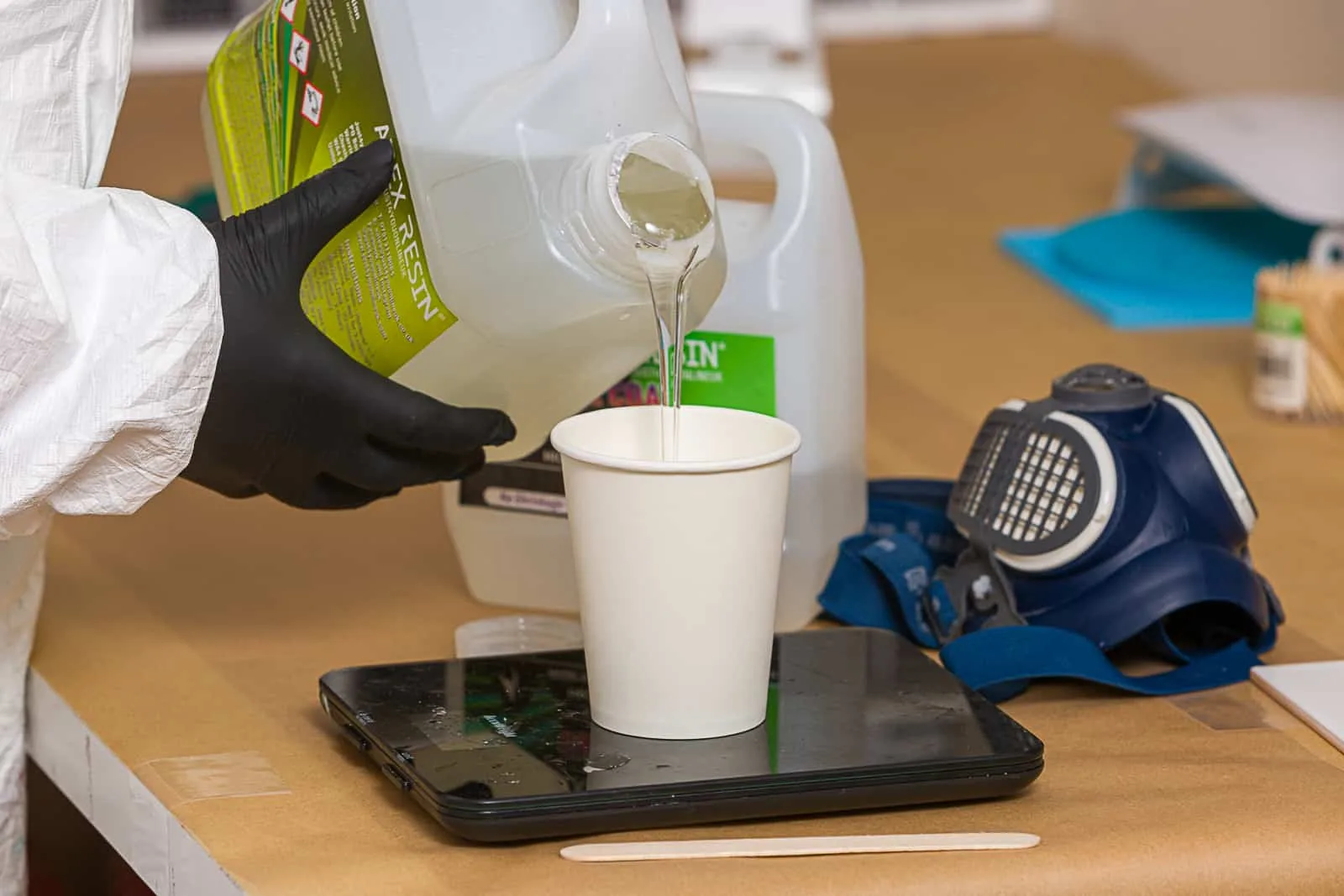
Where do you get your inspiration from?
There isn’t anywhere special. Observing nature and experimenting with colour combinations is often a starting point. What I enjoy the most is when a customer asks me for something specific, that kick starts my creativity. Hearing the story behind the request, or why something has a personal connection, is fantastic as a way to guide me in creating something special for them. That can be really fulfilling creatively.
Is that just for jewellery?
No, it can be anything. I recently had a lady ask me to make a trinket pot for her daughter who is called Daisy. She was talking to me about the colours that she would like to be included, without realising that I could include real daisy flowers. So we were able to combine our ideas and I made a completely different trinket pot, in a style that I hadn’t made before.
What size is a trinket pot?
Hmmm, roughly 8-9cm wide. Just large enough to fit some loose change, or jewellery items.
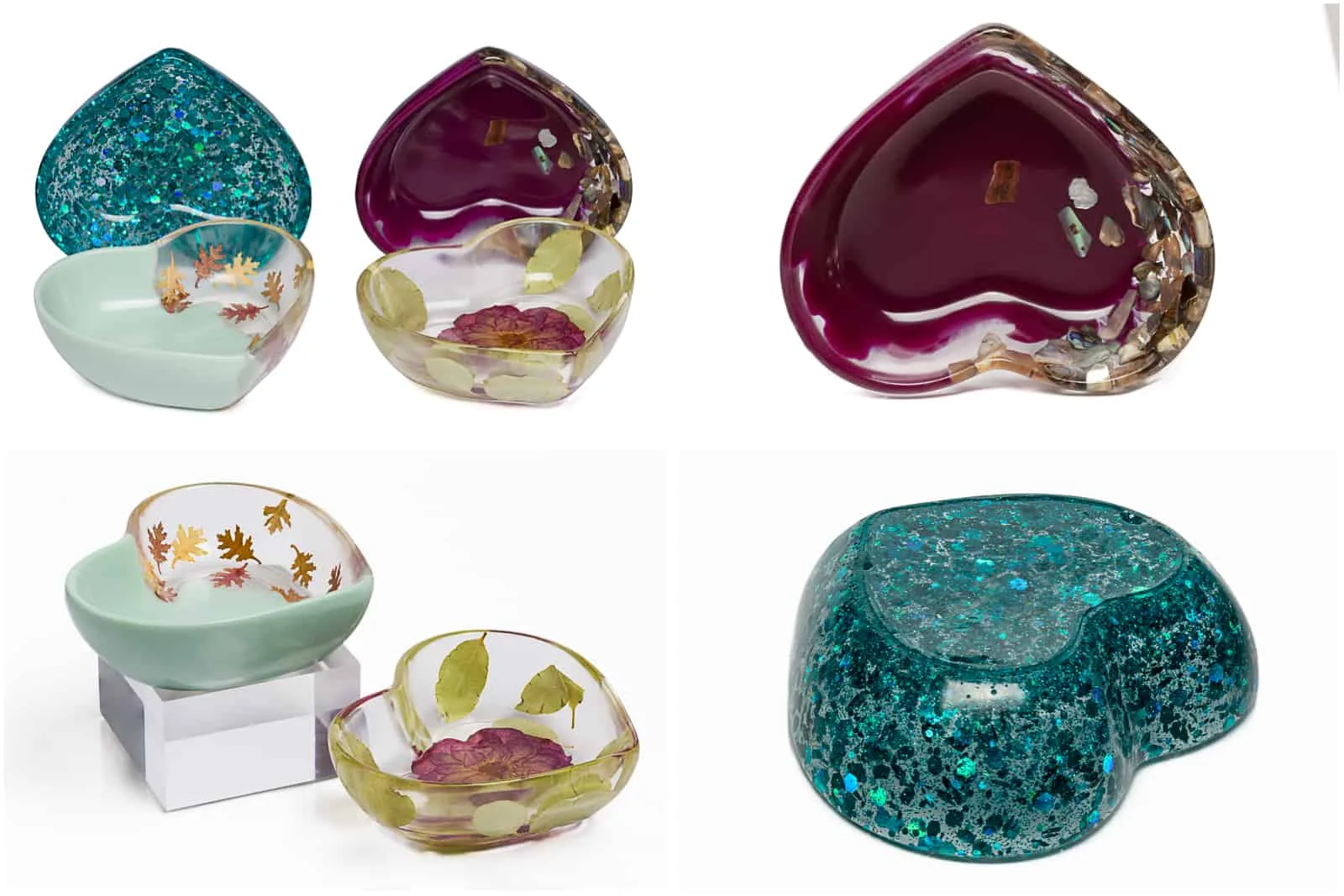
How long does it take to make one of your products, is it hours, days …?
Pots and bookmarks can take up to three days for the resin to properly cure [set], although it’s touch dry after a couple of hours. The ultra-violet activated resin, that I use for some of the earrings, shortens the production time because they cure under the light. But that’s offset by the fact that they are a lot fiddlier to work with due to the small size, trimming the flowers, and getting the placement just right.
What about the time for UV resin to cure?
The resin is built up in layers, but it takes about four minutes in total per layer, using a UV Lamp.
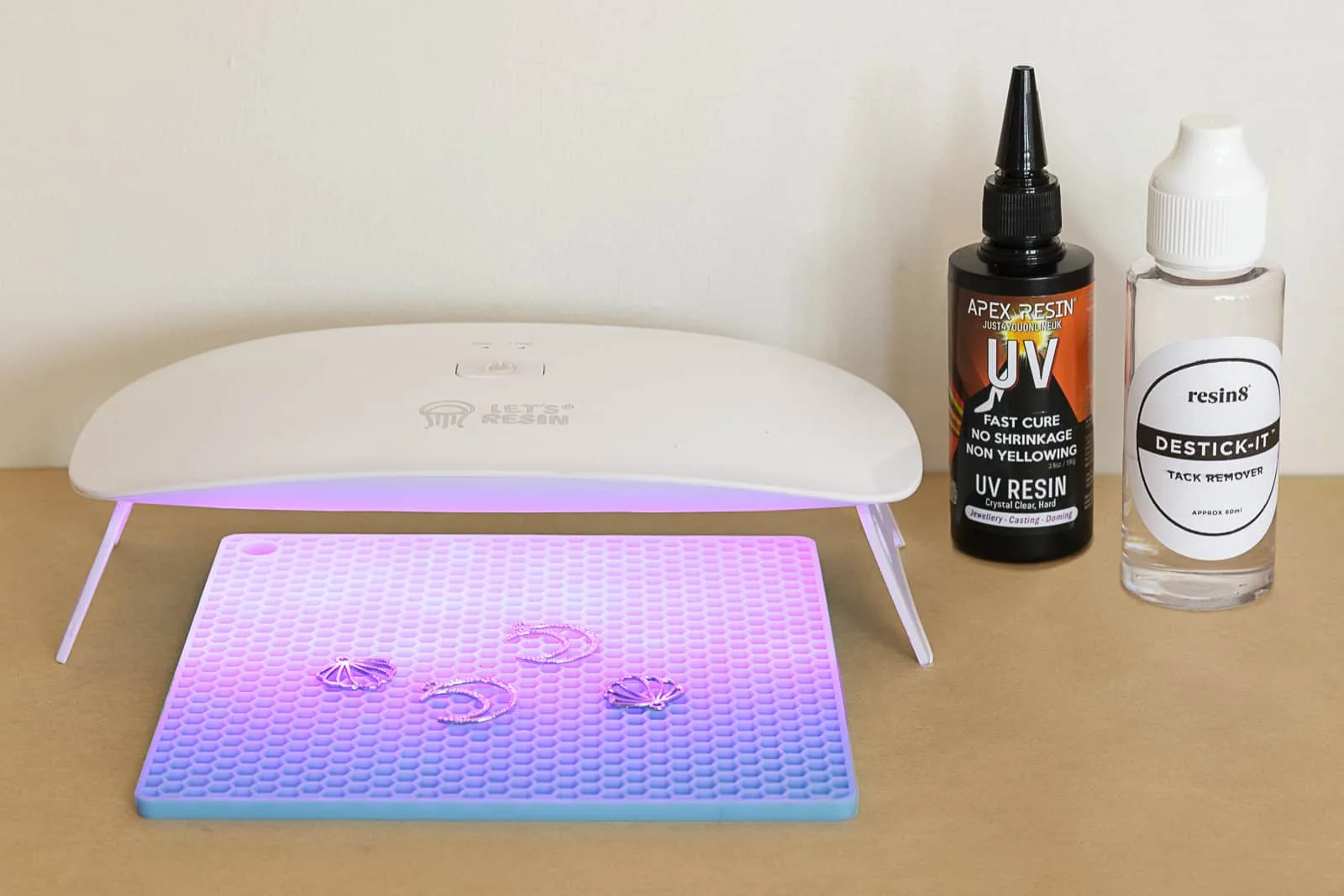
Is storage a problem? It tends to be for most small businesses that supply goods.
[Laughs] I think I’m just getting to the stage now, where it might be soon!
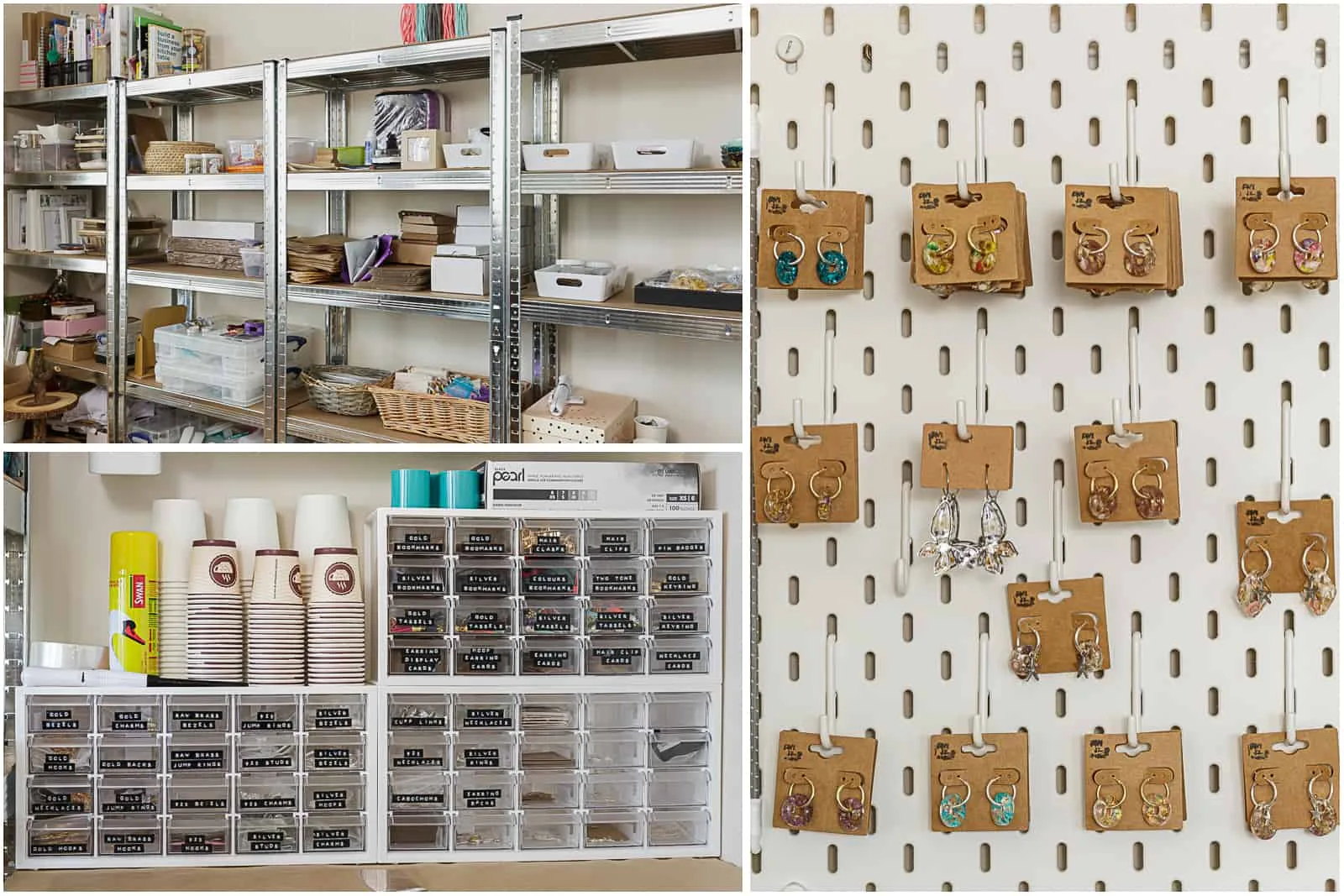
Do you have a special area for the curing process?
I have space set aside in my work area, but it has to be kept ultra clean and covered. I learnt that to my cost early on. I woke up one morning to find fly footprints all over one of my earrings! [Laughs]
I woke up one morning to find fly footprints all over one of my earrings!
Are there any health and safety considerations when working with resin?
Yes, and it was something that I wasn’t aware of starting out. It took a while before I realised that the skin irritations I was experiencing was a direct result of handling the resin. These days it looks like I’m on the set for some Science Fiction horror film when I’m working. I have a full on Hazmat suit, face mask and gloves that I wear. Even when I’m tidying up the day after a production day I wear protective gloves.
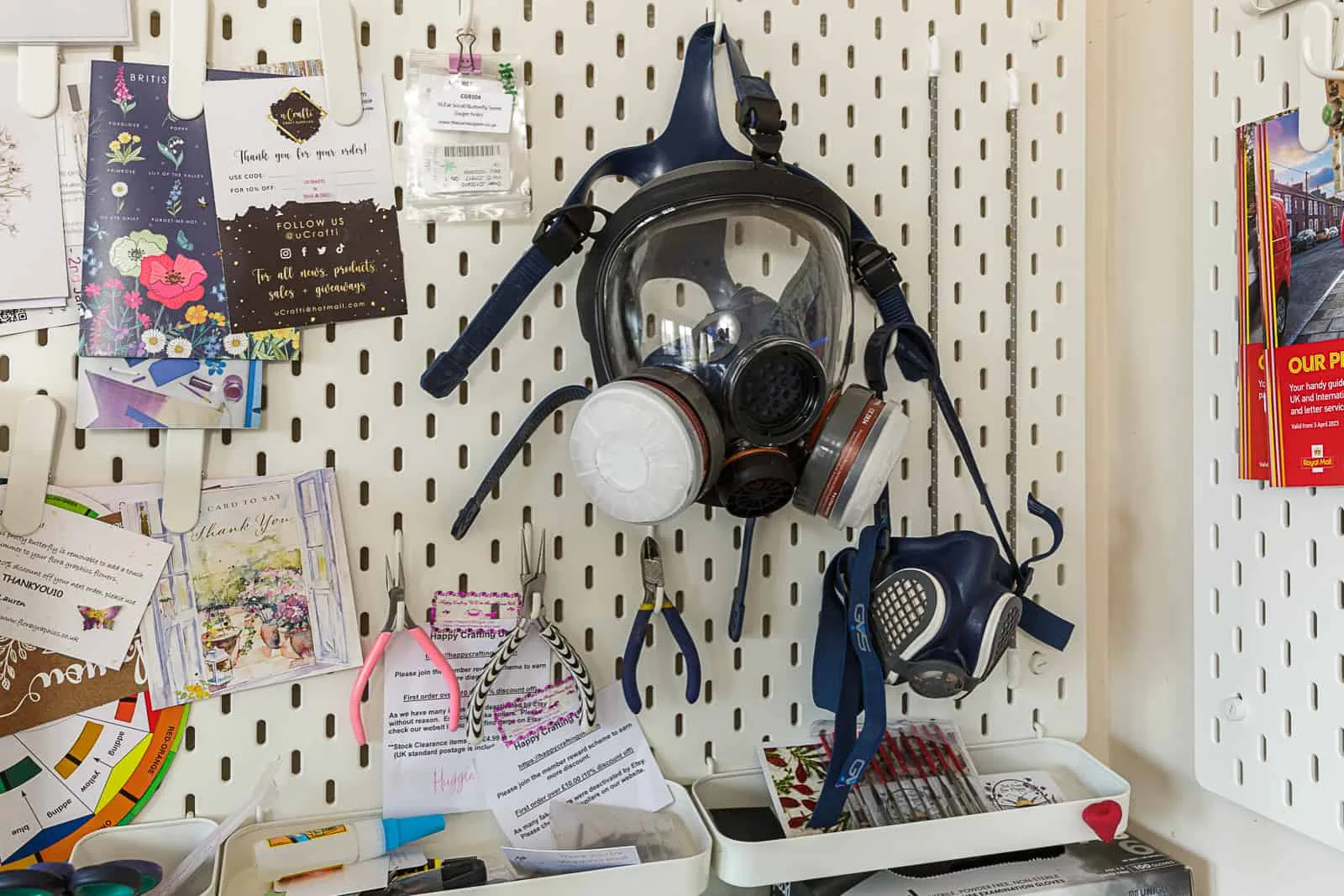
Reference [HAZMAT]
HAZMAT is an abbreviation for “hazardous materials”—substances in quantities or forms that may pose a reasonable risk to health, property, or the environment. HAZMATs include such substances as toxic chemicals, fuels, nuclear waste products, and biological, chemical, and radiological agents.
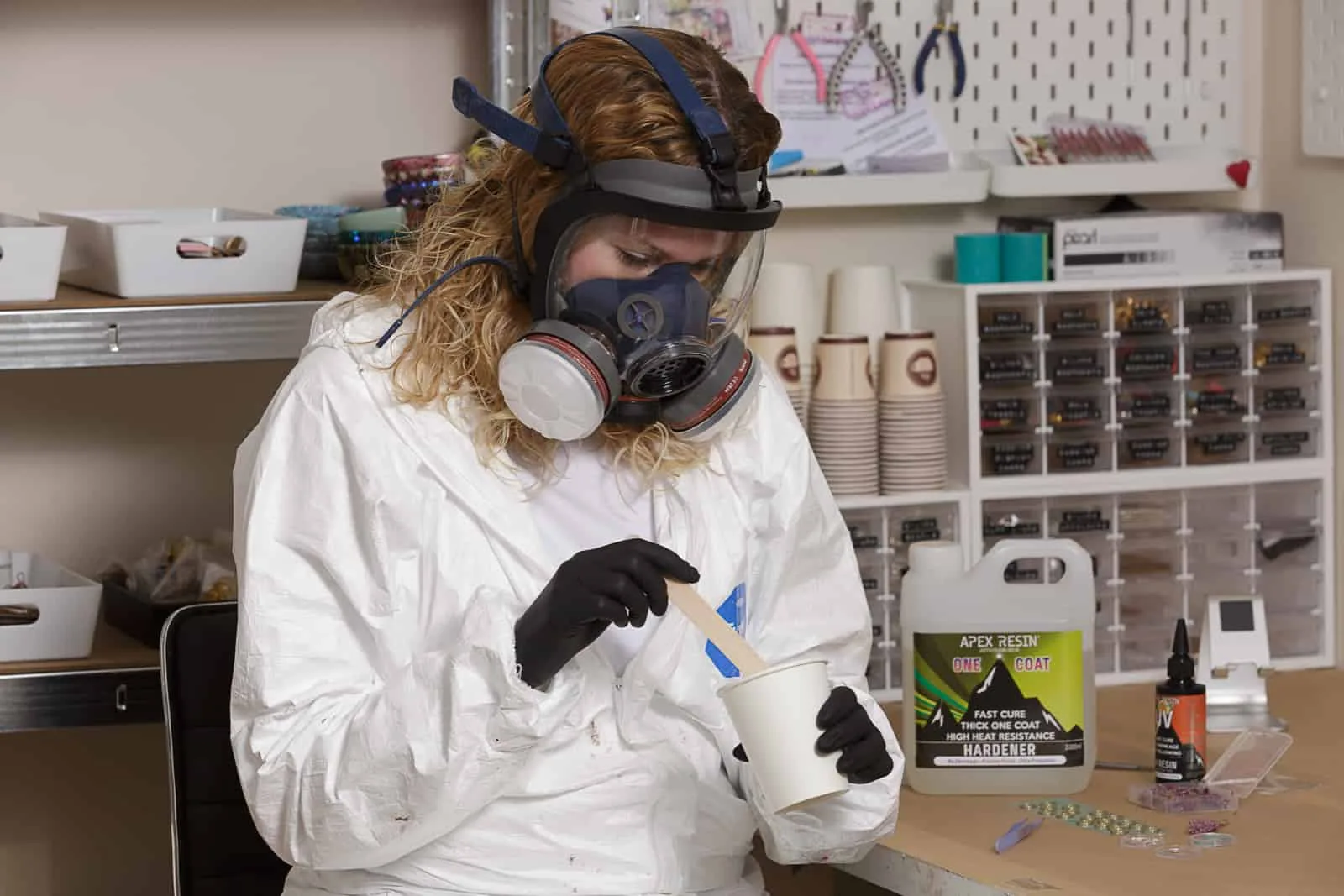
Sounds like fun! [shocked]
[Laughs] It’s not a problem once the resin has cured of course, it’s only during the initial resin mixing stages when it’s still in liquid form. I wear the protection and have open windows during that time for ventilation. That also applies during sanding, that’s a given. Obviously no-one else can be in the working area unless they are also wearing protection.
But you only work with small quantities at a time?
I usually only make up about a coffee cup full of resin to work with in one go, because it’s a race against time before it starts to cure [set]. That amount doesn’t go that far when creating pots and bookmarks, so I have to keep reheating the resin. When I first started I didn’t have that many moulds, so it would take me a lot longer to make my stock. I’ve built up quite a collection now but they have a limited life span.
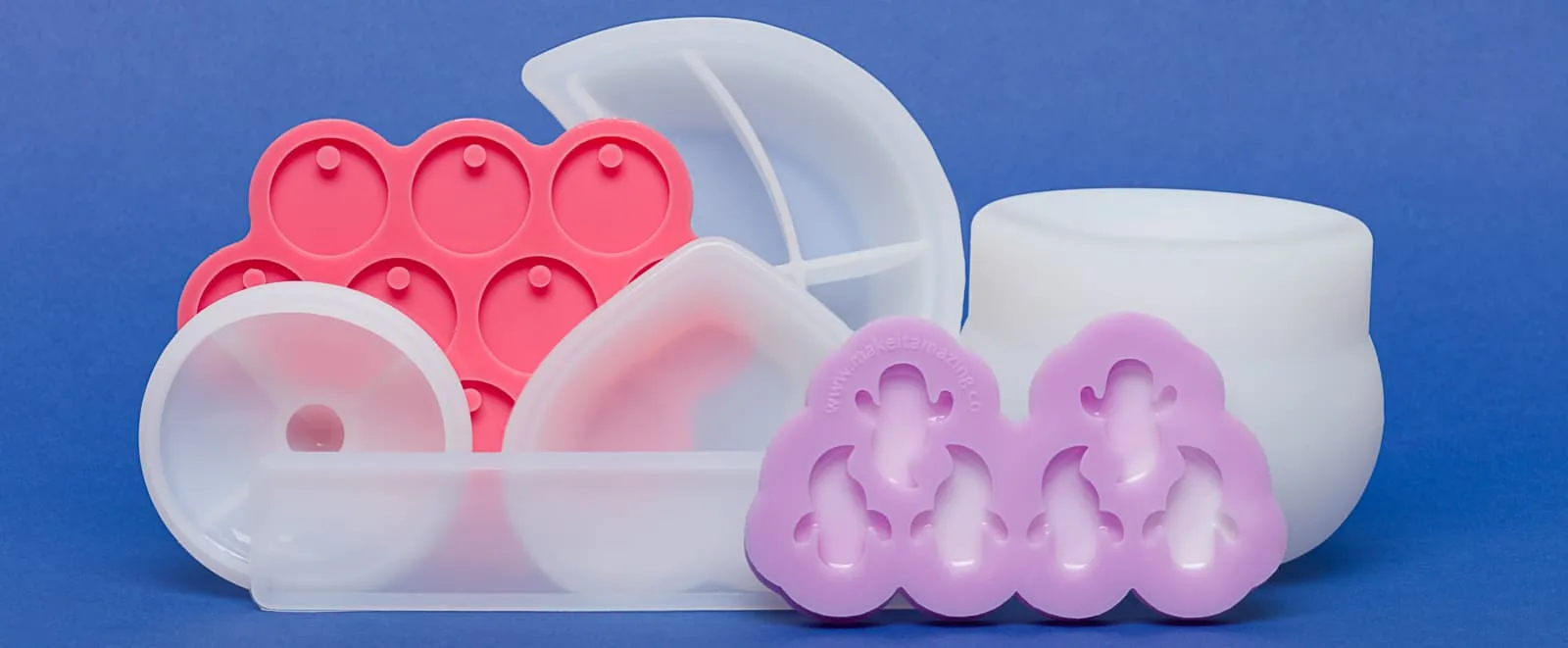
Oh, do they wear out quickly then?
They’re made of silicone and have a coating which helps the final finish to be shiny. Once the coating has deteriorated the mould has to be replaced. The manufacturers advise about eight uses for each mould, so the costs can quickly mount up
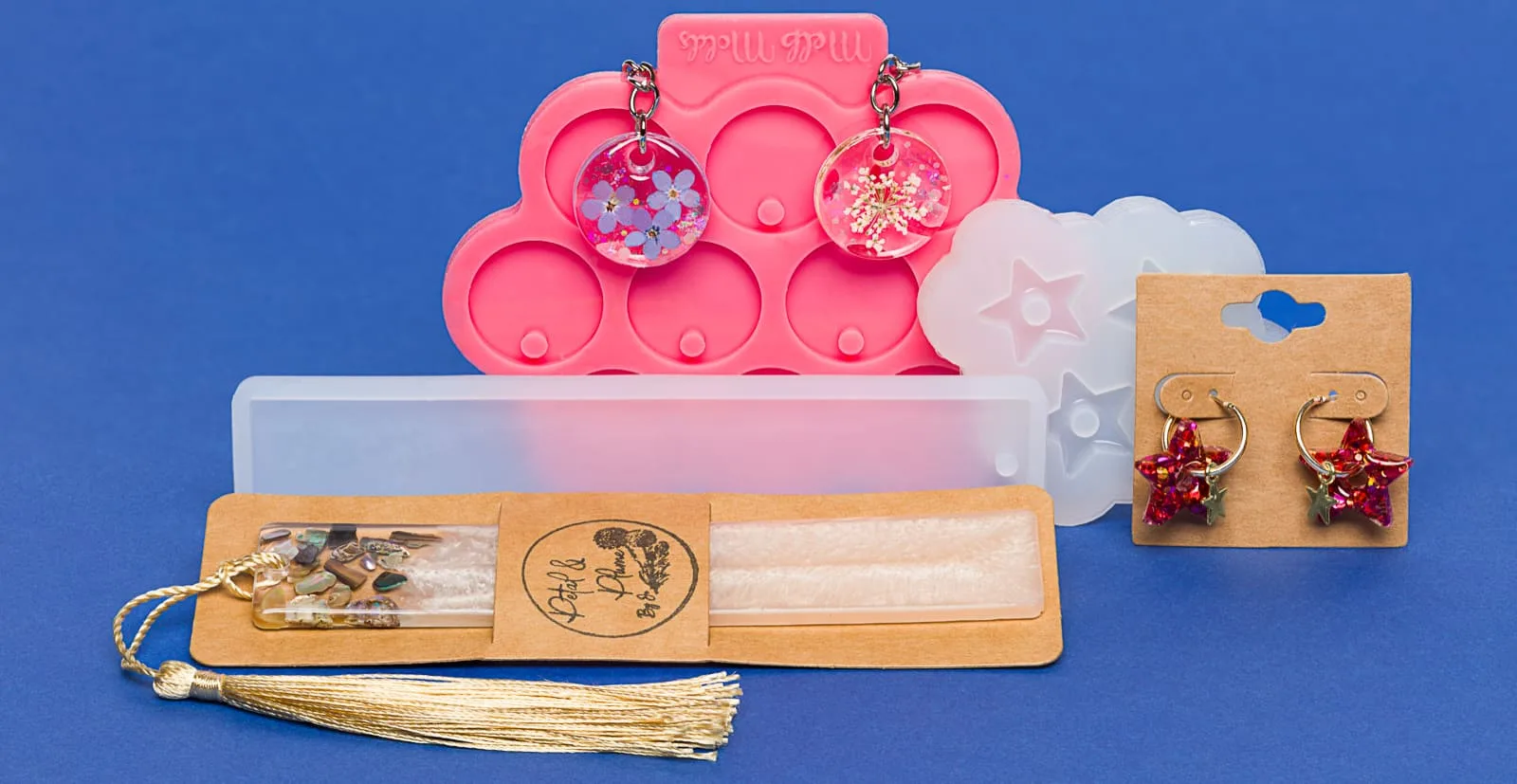
In the last part of Jo’s story, we talk about sales and marketing. Watch this space.